Employee Spotlight: José Fuentes
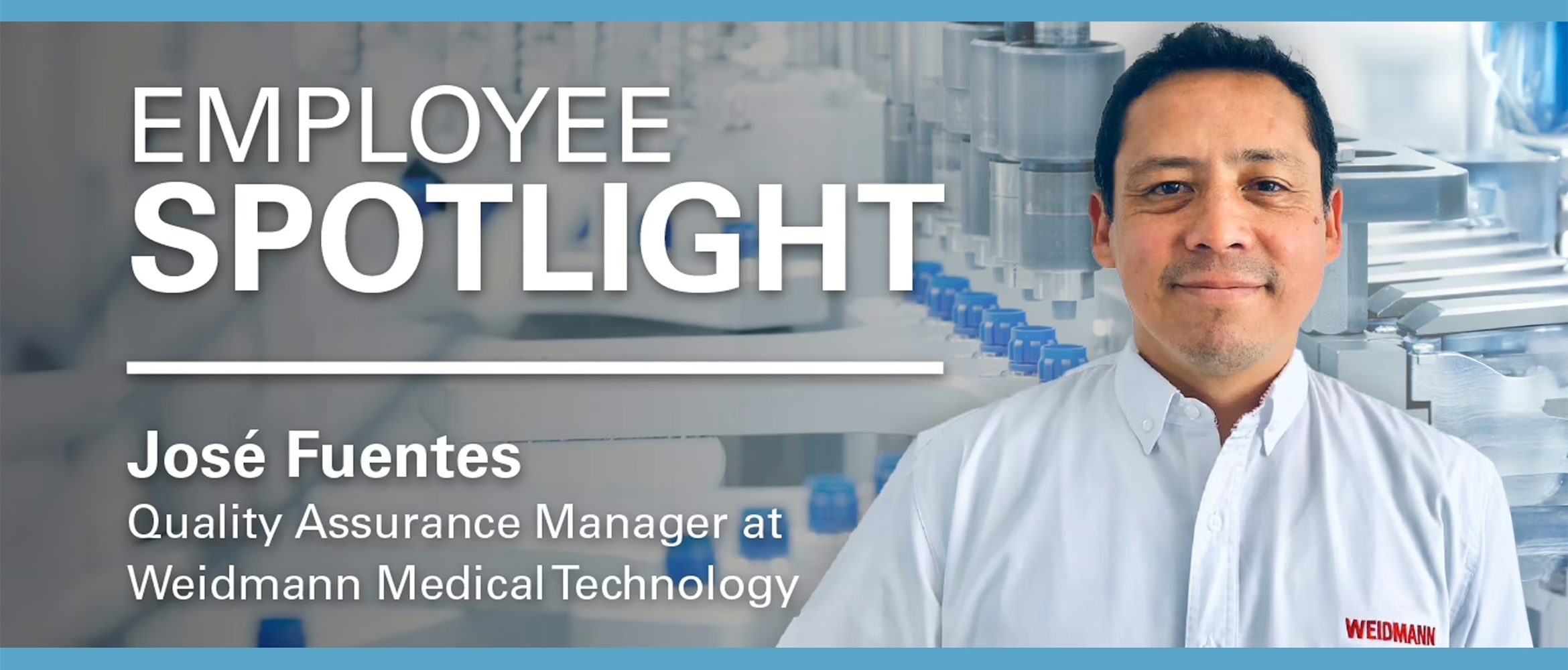
Clean Room Expansion in Saltillo: An Interview Series with José Fuentes
José Fuentes, our Quality Assurance Manager at Saltillo, Mexico, visited Switzerland at the end of November 2023 to prepare for a significant project establishing new production lines in Rapperswil and Saltillo. During the first part of this interview, he discusses the key quality issues addressed during the visit and the training received for the project in Mexico. The focus is on understanding and replicating quality processes between Switzerland and Mexico.
Viola Frey
Hi José, it’s good to sit down to talk with you today. Can you tell us a little bit about yourself?
José Fuentes
Hi Viola, sure, I’m a Chemical Engineer from Mexcio City and have worked for Weidmann Medical for four years. I started in November 2019, just before the pandemic. I’m married and I have a 6-year-old son. My wife is an Industrial Engineer and works in the automotive industry, which is the main industry here in Saltillo.
I have been working in the pharmaceutical and medical device industry for 23 years, always from the quality side but always in a very dynamic way with the production or operations departments. So, I joined Weidmann Medical as a Quality Assurance Manager and have enjoyed my time here since starting.
Viola Frey
So José, you have been to Switzerland for this new project?
José Fuentes
Yes, I was there at the beginning of November 2023. During our visit, we spent one week between both facilities, Bad Ragaz and Rapperswil.
Viola Frey
What was your primary purpose for visiting Switzerland?
José Fuentes
We used the visit as an opportunity to learn as much as possible. Most importantly, we wanted to discuss the key quality issues that are of the highest priority. To further our insights, we met with the entire quality team, led by the Director of Global Quality, Dr. Jens Maximilian Friedrich. These conversations helped to build our knowledge of what quality processing looks like in Switzerland compared to Mexico. We also took the opportunity to receive training to help with the project of setting up new production lines at the Rapperswil and Saltillo sites.
For this training, we spent two days in Rapperswil, mainly reviewing the new production processes and touring the facilities. We also saw the new machines in operation; they were running as part of the project set-up.
In addition, we reviewed the quality aspects, including strategy issues, for this new customer project. We learned about documentation and test methods we need to implement here in Mexico for a successful technology transfer from Switzerland to Mexico.
In that sense, we plan to reproduce not only the production processes but all the quality aspects. Specifically, we have to develop every single testing method here in Mexico. We will standardize the testing methods in Switzerland and Mexico according to the work our colleagues in Switzerland have done in the past.
Viola Frey
Is the project in Mexico basically a twin of the Rapperswil project?
José Fuentes
That’s correct.
Viola Frey
How long did it take you to build the clean room, from planning to finishing it?
José Fuentes
We started in March 2023 this year and finished in August 2023.
Viola Frey
So that’s pretty quick, isn’t it?
José Fuentes
Yes, indeed, it took about six months and was an impressive project building construction.
Viola Frey
How was the project set up for the new clean room?
José Fuentes
We had a project leader from Mexico, Lourdes Labastida, our project manager. From the Swiss side, Roger Wolf from the technical department supported us. I was responsible for all quality issues.
Viola Frey
What were the main challenges in meeting all quality requirements according to ISO 13485?
José Fuentes
The real challenge from a quality perspective is demonstrating that once the new clean room is built and completed, it will be classified according to ISO 13485:2016. So, in that sense, we achieved our initial clean room certification from an external company that was in charge of a series of tests performed to show that it was operating at its required class.
The certification process checks the following parameters: temperature, humidity, pressure, and degree of purity (suspended dust in one cubic meter of air). It also checks whether the contamination class, air velocity, pressure, and flow rate comply with the project requirements.
From my perspective, this was the biggest challenge in building the new clean room, as quality is Weidmann’s top priority. Our unwavering commitment guarantees that every product is crafted to precise specifications, prioritizing patient care throughout the process.
Viola Frey
So, did this external company that was checking all those parameters issue official documentation to verify the clean room’s proper functioning?
José Fuentes
Yes, the documentation issued ensures that our new clean room complies with ISO and current Good Manufacturing Practices (cGMP) standards.
- A note: As this is a new clean room, the state of the clean room occupancy falls under “as-built,” i.e., a brand-new clean room environment that has never been used. In this state, the room is at its cleanest. The installation is complete, and the services are functional, but no materials, production equipment, or people are present.
Viola Frey
It was a very quick project, but were there any difficulties along the way when you thought there would be delays, or were there any unexpected challenges in building the clean room?
José Fuentes
I have to say that it was really impressive since everything within this particular project was according to the timeline.
We didn’t have any real problems from a quality point of view because we were able to separate the new clean room construction from the current series production, which meant that they didn’t interfere with each other, e.g., the warehouse, material flow, packaging materials, or finished goods. That made it easier to manage and allowed us to meet the schedule.
Viola Frey
What do you think made the project so smooth?
José Fuentes
It was also very important for us to have the support of the Swiss team at all times. To accomplish this task, we received a lot of feedback from the quality department and the project manager responsible for the project in Switzerland.
Viola Frey
Thank you for your time today. I look forward to our next catch-up about sustainability considerations for the clean room and future plans.
Viola Frey
Let’s talk about sustainability. Are there any new requirements you must meet to fulfill any sustainability issues, or is there anything you can do to be more sustainable with the new clean room?
José Fuentes
In terms of sustainability, maintaining the clean room’s ISO A classification after qualification is important.
This means that once we have the qualification, we must maintain the right conditions to avoid anything out-of-specification in those particular areas, such as temperature, particles, or contamination.
In this sense, the situation of the cleanroom at the beginning is that there is nothing in it. We have no equipment or operations, so we only need to enter the cleanroom once we receive all the machines and production lines. We received some of the machines in mid-January, and that’s when we had to make the appropriate preparations to avoid contamination when we started moving all the production equipment into the cleanroom. A second qualification or re-qualification will be required once we have all the equipment in the cleanroom.
Viola Frey
And when will that be – at the end of 2024?
José Fuentes
Yes, by the end of this year, or, let’s say, Q4/2024, we expect to have all the equipment inside the clean room and to achieve the re-qualification.
The re-qualification aims to demonstrate that the clean room meets the requirements according to the ISO standard of classification A with all the equipment inside the clean room.
Viola Frey
Will you be responsible for quality when the machines arrive and production starts?
José Fuentes
That’s exactly right. From a quality perspective, we are involved even when we are not producing. But it is necessary to maintain the conditions of the clean room in terms of good manufacturing practices or GMP standards.
Viola Frey
What is the size of your quality team in Mexico?
José Fuentes
At the moment, we have six people on the quality team:
Besides myself as the Quality Assurance Manager, we have four Quality Technicians and one Quality Engineer on the team, who also came with me to Switzerland for training. We are also considering hiring two additional Technicians and one Quality Assurance Engineer for the project. This will be not only for the project but also for the regular production once we have the product in production, and certainly for the rest of the products we make.
Viola Frey
When planning the clean room, did you consider applying Six Sigma and lean manufacturing standards, as these are our usual standards?
José Fuentes
Yes, since this project involves transferring technology from Switzerland to Mexico, we have the great advantage of the experience that the Swiss team has gained over the last month. So, from a planning perspective, we have a design of the warehouse’s layout, including the clean room and the auxiliary areas that will provide services to it. For example, the raw material feed, which will be located next to the clean room, is included in this layout.
This will be very efficient for the process. The intention is to have a lean process from the beginning and avoid any significant improvements needed before the process’s release. Later, once we start producing the new components, continuous improvement will be in place. Our starting point will begin with the baseline from the Swiss production line.
Viola Frey
What do you see as the biggest challenge in this project?
José Fuentes
Well, the biggest challenge from a quality perspective is that at the end of the project, before we start regular production, we can show that the Saltillo site can produce quality parts based on customer requirements.
Viola Frey
That’s the beauty of this project, right? To serve the European market from Switzerland and the North American market from Mexico. So this clean room is dedicated to one customer, but with the remaining capacity at the Saltillo site, we have room to expand, and more customers could benefit from this: Swiss quality – made in Mexico.
José Fuentes
That’s true! The whole team in Mexico is committed to this project and loves being a part of it. They all want to show how well we can execute, so we look forward to finishing the project and getting into regular production. I am very proud of this team.
Viola Frey
Thank you very much for the interview, José.